

If someone get's it working that would be cool. I'd love to be able to use more modes on the Gyre (Automatically) Any feedback from guys with electronic experience, especially RC knowledge would be appreciated. I have not ordered anything yet, I thought I would bounce this off you guys first before I take the leap. Many of the ESC's are programmable, so you can tailor it to your specific need, I am just not sure if it will be adaptable enough to operate the Gyre.
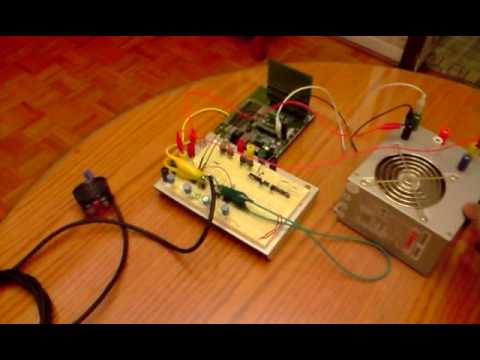
Have to see if the onboard microcontroller in them is able to adapt to do low speed control as well. The hobby ESC's are also normally paired with the outrunner motors that spin FAST (like 210K RPM). 20A is the smallest common ones, with a few 10A ones as well. All the ESC's support much higher current limits than I expect to need. There is also the question about limiting the current through the coils of the Gyre. I am thinking I might be able to get away with 18V (the highest rated ESC I found listed 22V as its limit). The occasional ESC description on eBay lists the actual voltage range that it supports, but most just list the size of LiPro and/or NiMH cells it supports. I expect I will have to run at a lower voltage than what the Gyre appears to use currently (24V) as the ESC's are all targeted at voltage ranges provided by battery packs (about 12V). Depending on the model of ESC, they offer both forward and reverse rotation and run sensorless (just what we need for the Gyre). So here is my plan, I am going to try to use a RC ESC to interface the Gyre to my controller. If they would work, they would fit my requirements exactly. Hmm, and these take a 5V PWM servo input, exactly what I have in my controller. Everything appears to line up with it being a Brushless DC Motor.Īfter googling around a bit and looking at the various Arduino based DIY projects to control BLDC motors, I remembered that I had seen lots of Brushless Electronic Speed Controllers on eBay intended for the hobby RC field. This would mean the coils are 2.35 ohms each and wired in a Wye configuration (as opposed to Delta). I measured the resistance between the 3 pins of the cable and found that any 2 pins are 4.7 ohms, and if I short 2 pins and measure with the 3rd pin, this is 3.6 ohms. I am pretty sure I have figured out it uses a Brushless DC Motor(BLDC).
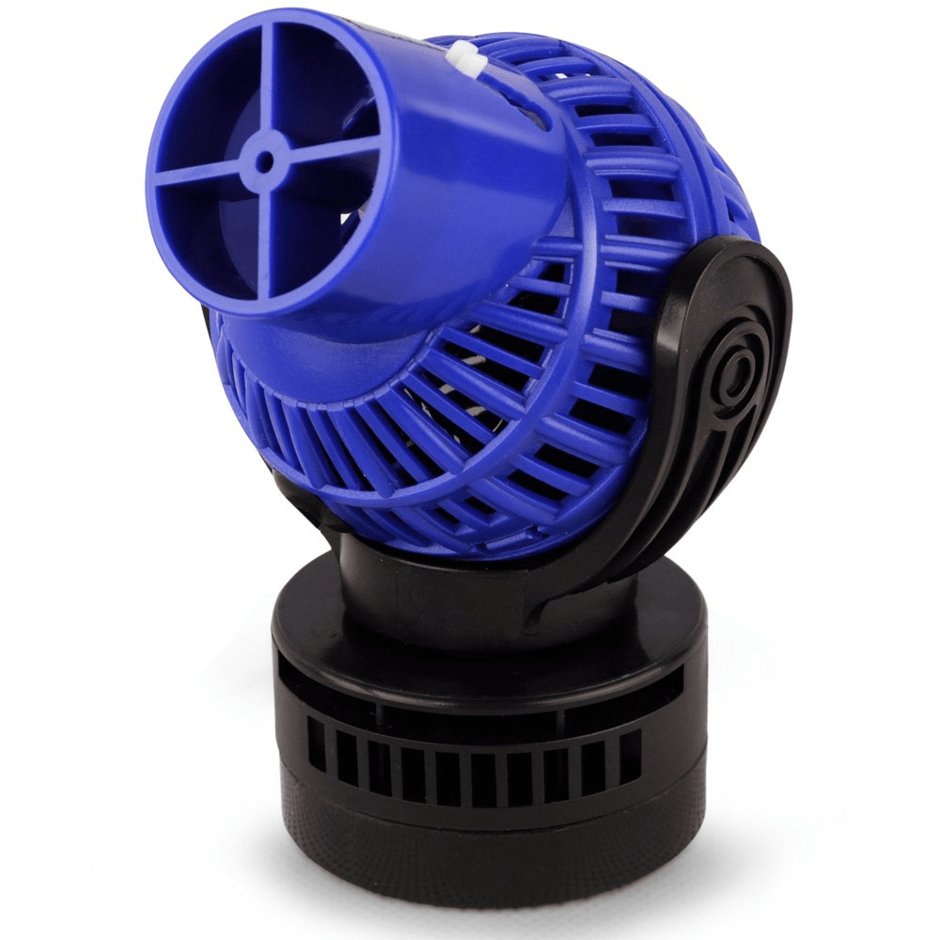
This got me to thinking about how the Gyre is operating, and more importantly, how could I replace the current controller with something that I can interface directly to. I know they are coming out with a Apex compatible controller, but since I use 5V PWM in my DIY system, I would need to build an interface just to be able to use the Apex module when it is available.
DIY WAVEMAKER CONTROLLER MANUAL
When you get used to your pumps slowing at night, shutting off at feeding time, or running in a preset pattern, going back to a manual controller just sucks. I just recently bought the Gyre and love the flow, but not having the pump controlled by my controller is a really bummer. I am more of a digital guy, so you old farts that are analog, please correct my limited analog knowledge. Please, if you have any questions don't hesitate to ask.I am posting this *before* I go down this path in the hopes that other (informed) DIY people can help fine tune my conclusions. Potentiometer: 10K Ohm Linear potentiometer The parts I used outside of the ones linked previously are as follows. Please be mindful of this, for a more permanent solution please look into using an arduino shield that you can solder to. Breadboards also are only really suitable for prototyping and are quite fragile, any sort of jostling can dislodge wires, cause wires to short against each other, etc. Please enclose your project in a box to protect from splashing. Also, please be aware we are also working near water. Also please remember, although you are working with low voltages you are still working with electricity, please be mindful that short circuits can still cause issues up to and including fires (although this is unlikely I still have to say this).
DIY WAVEMAKER CONTROLLER INSTALL
do not install into your tank until everything is working correctly. Please lay everything out on a table and test.
